LabStrong™ Rapids™ Help Code H005 | Troubleshooting
You have been directed to this page because you scanned a QR code on the LabStrong™ Rapids™ Type I Water Purification System.
A printed copy of the troubleshooting document can also be found in the user manual that was included with the shipment of the Rapids™ system.
Product water flow rate is too low.
Possible Causes & Solutions
The inlet water pressure has dropped or stopped. Check the inlet water shut off valve, (failed valve) PM0033-6. | The inlet water flow rate has dropped. Check the inlet water filtering system for a clogged filter. | The 0.2 micron Final Filter could be clogged. Replace the 0.2 micron Final Filter (FL0016-1).
Shop Parts
Product water continues to flow water from dispenser after releasing the dispense button.
Possible Causes & Solutions
The 0.2 micron final filter could be clogged. Replace Final filter (FL0016-1). | Dispense solenoid valve could be defective. Replace the dispense solenoid valve (PM0033-3).
Shop Parts
No product water flow from dispenser.
Possible Causes & Solutions
No flow from inlet water source. Check the inlet water, at feed source. | Feed water not connected. Connect feed water source to Rapids™ unit. | Failed inlet solenoid valve. Replace inlet solenoid valve (PM0033-6). |
The 0.2 micron Final Filter could be clogged . Replace the 0.2 micron Final Filter (FL0016-1)
Shop Parts
Short cartridge kit life.
Possible Causes & Solutions
Cartridge kit is beyond expiration date. Check expiration date. Cartridge kits begin to lose capacity after being stored for two years from the date of manufacture. | Poor quality feed water. Check the quality of the inlet tap water source, TDS, Turbidity, Silica and conductivity.
Shop Cartridges
Recirculation water will not rinse up to desired purity level.
Possible Causes & Solutions
Exhausted cartridge kit . Replace cartridge kit as indicated in, "Cartridge Kit Replacement". | New cartridge kit installation . Check to make sure that the each cartridge from the kit is placed in the proper order. Position #1 through #4 and in the proper orientation, top and bottom. Rapids system is a down flow configuration.
Shop Cartridges
Water leak at one of the cartridge connection fittings.
Possible Causes & Solutions
Check to make sure the fitting is pressure down on the cartridge nipple as far as possible. Depressurize the system, (relieve the water pressure) then remove the fitting that is leaking and re-seal the fitting back to the cartridge to seat the o-ring in the fitting to the cartridge nipple securely .
Technical Assistance
Exhaustion Threshold error message "Cartridge Kit nearing Exhaustion".
Possible Causes & Solutions
The cartridge kit has reached its exhaustion threshold preset to factory setting of, 17.9 Meg-ohm/cm. Compare the value of the exhaustion threshold to the purity reading on the display. | The exhaustion threshold has been adjusted to a different value at location. Contact LabStrong™ for technical assistance.
Technical Assistance
Purity reading is displaying above 18.2 Meg-ohm/cm.
Possible Causes & Solutions
The temperature compensation has been disabled. Set the temperature compensation mode to "On". This will compensate the purity reading to 25° C.
Technical Assistance
Error codes appear on the display, but cannot be resolved by changing the values.
Possible Causes & Solutions
One or more values have been changed causing error codes that cannot be resolved. Press the Menu button, then press the Settings button and this will lead to the Factory Reset button, once this button is pressed the RESET button will appear. Press the reset button to reset all of the Factory Values back to the original settings.
Technical Assistance
Contact our Technical Service Team for one-on-one assistance.
Every lab is different and has its own unique needs. Our Technical Service Team is ready to help you. Contact us via email or phone. You may also find helpful how-to videos on our YouTube channel.
- technicalservice@labstrong.com
- 563-588-8900
- Monday – Friday; 8:00 am – 5:00 pm CST
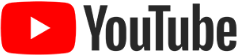